Text Copied!
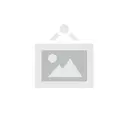
wireman
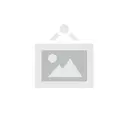
wireman
59
Applications
Text Copied!
About the Job
Skills
PCB (Printed Circuit Board) wiring refers to the process of designing, laying out, and connecting electrical circuits on a printed circuit board. PCBs are used in virtually all electronic devices, from smartphones to computers, and are a crucial component in modern electronics. "Wiring" on a PCB refers to the electrical connections, or traces, that connect different components on the board, such as resistors, capacitors, microchips, and other electronic components.
The process of designing and manufacturing PCB wiring involves several critical steps, which I’ll break down here:
1. Designing the PCB Wiring (Circuit Design)
Before you can create the actual wiring on a PCB, the circuit design must be planned out, usually through software that allows for schematic design and PCB layout. Here are the steps involved:
Schematic Design:
- The first step in creating a PCB is to design the schematic diagram. A schematic is a representation of the electronic circuit, showing all the components (resistors, capacitors, ICs, etc.) and how they are connected.
- This design is done using electronic design automation (EDA) software such as:
- Eagle
- KiCad
- Altium Designer
- Autodesk Fusion 360
- OrCAD
- The schematic will define the electrical connections between components, but it doesn’t specify the physical layout on the board yet.
PCB Layout:
- Once the schematic is ready, the next step is the PCB layout. This involves taking the schematic and placing the components onto a physical PCB layout. This is done using the same EDA software.
- The PCB layout specifies the exact locations of each component and how they are connected with traces (electrical paths that connect components).
- The software ensures that the traces don't overlap, are routed efficiently, and comply with the constraints of the board (such as size, layer count, and electrical requirements).
Key Considerations in PCB Layout:
- Trace Width: The width of the traces must be sufficient to carry the expected current without overheating. The width of traces is determined by the amount of current they need to carry and the board's material properties.
- Trace Routing: Traces need to be routed efficiently to minimize interference and ensure signal integrity. The routing can be done manually or automatically by the software.
- Ground and Power Planes: Proper ground and power planes are necessary for stable operation, especially in high-frequency or high-power circuits.
- Clearances: The spacing between traces must meet the standards specified in the design rules, to prevent short circuits or electrical interference.
2. Creating the PCB (Manufacturing)
Once the PCB design is complete, the next step is to manufacture the physical board. Here’s how the PCB is created:
Material Selection:
- The base material of the PCB is typically made from fiberglass (FR4) or other composite materials that provide mechanical strength and electrical insulation.
- The conductive material (copper) is used to form the traces on the board.
Printing the PCB Layout:
- The PCB layout is transferred to the board using a process like photolithography.
- The copper is first coated with a light-sensitive material called a photoresist.
- A photomask (essentially the PCB layout design) is then exposed to UV light, causing the photoresist to harden in areas not covered by the mask.
- The unexposed photoresist is washed away, leaving the desired circuit traces on the copper layer.
Etching:
- The exposed copper areas are chemically etched away using a solution that removes the unwanted copper, leaving only the traces that were protected by the hardened photoresist.
- The remaining photoresist is then removed, leaving just the copper traces on the PCB.
Drilling:
- Holes are drilled for components that need to be inserted into the PCB (e.g., through-hole components like resistors, capacitors, and connectors).
- This step is also important for via holes, which are used to connect traces between different layers of a multi-layer PCB.
Soldermask and Silkscreen:
- A soldermask layer is applied to protect the copper traces from oxidation and to prevent solder from bridging connections during the assembly process.
- A silkscreen layer is then printed on top of the soldermask, showing the component labels and other information on the PCB surface.
Testing and Quality Control:
- After the PCB is manufactured, it undergoes testing to ensure that the electrical connections are correct and that there are no faults or shorts in the wiring. Common tests include automated optical inspection (AOI) and electrical testing (e.g., in-circuit testing (ICT) or functional testing).
3. Assembly and Wiring of Components
After the PCB is manufactured, the next step is to assemble the components onto the board. This process includes:
Soldering:
- Components are placed on the board, and their leads or pads are soldered to the traces.
- Surface-mount technology (SMT) is commonly used for modern PCBs, where components are directly mounted on the surface of the PCB. Through-hole technology (THT) is used for components with leads that go through the board.
- Solder paste is applied to the pads, components are placed, and then the assembly is passed through a reflow oven for SMT or manually soldered for THT components.
Wiring Components:
- In some cases, particularly with prototype boards or complex designs, wires (or jumpers) are used to make connections between components that can’t be directly routed using the PCB traces. This is often done during the prototype stage or when specific connections need to be manually adjusted.
4. Common Challenges in PCB Wiring:
- Signal Integrity: High-speed circuits, such as those used in RF (radio frequency) or high-frequency digital systems, may experience signal degradation due to improper PCB trace routing, impedance mismatch, or crosstalk.
- Power Integrity: Ensuring that the power supply to components is stable, with minimal noise and ripple, is crucial, especially for sensitive electronics.
- Thermal Management: Power dissipation in the form of heat can affect the performance of the PCB. Proper trace design, heat sinks, and sometimes active cooling (e.g., fans) may be required.
Summary: PCB Wiring
PCB wiring refers to the process of designing and routing electrical traces to connect components on a printed circuit board. It involves designing the schematic, laying out the board, manufacturing the PCB, and assembling the components. Key considerations include trace width, routing efficiency, and ensuring proper electrical and thermal performance. The process is typically supported by specialized design software, and the final PCB must be tested for quality and functionality.
Let me know if you'd like more information on any specific aspect of PCB wiring or design!
About the company
Industry
Executive Offices
Company Size
11-50 Employees
Headquarter
Palghar, Maharashtra
Other open jobs from AtoZ Virtual
Machine operator (Lathe Machine operator)
AtoZ Virtual
+4 More Skills
Posted on December 04 2024
CNC Operator
AtoZ Virtual
+4 More Skills
Posted on December 03 2024
Laser operatore
AtoZ Virtual
+4 More Skills
Posted on November 30 2024
Machinist
AtoZ Virtual
+4 More Skills
Posted on January 30 2025
Turner
AtoZ Virtual
+3 More Skills
Posted on January 08 2025
Powered By
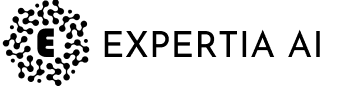